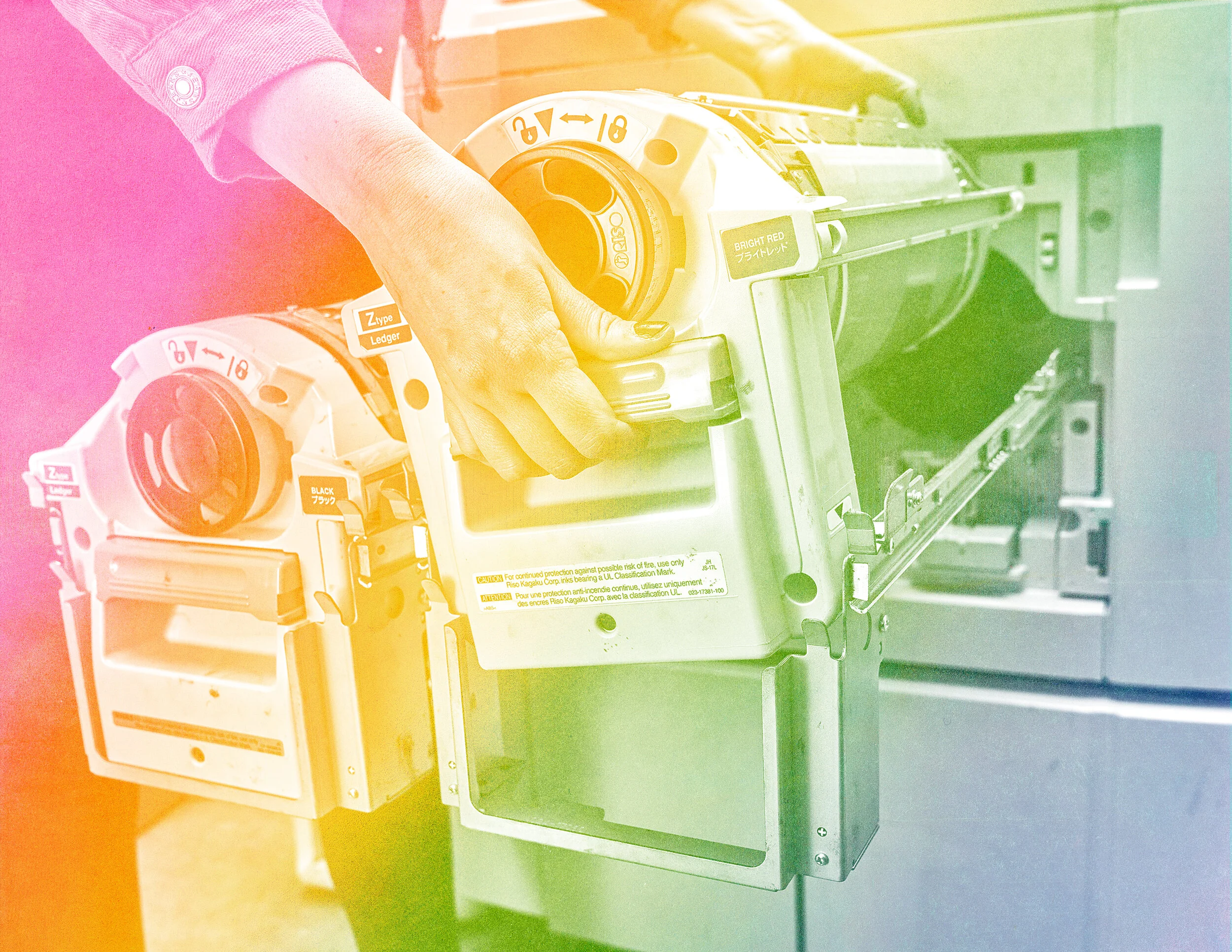
What is Risograph?
It’s like if Xerox and silkscreen printing had a baby
Riso evolved from mimeograph printing circa the 1950s when inventor Noboru Hayama first developed the organic ink formula and eventually the automation of the printing process with the Risograph press.
Inventor of Riso, Riso Weekend, 2021
Crimson, Medium Blue, on Golden Rod paper
Risographs typically print colors one at a time (some machines can print two colors) by feeding sheets of paper under a spinning drum wrapped with a disposable stencil inked with soy or rice oil-based inks. These oils hold onto pigment beautifully and create a variety of vibrant and fluorescent colors with luminous transparency.
Overlaying multiple colors mix to create a wide spectrum of new shades.
Two Color Test, Center Color Tests, 2020
Flo orange, blue, on white paper
My Printing Philosophy
Before discovering Risograph I almost exclusively screen-printed my work. Not much of a painter, the meticulous nature of layering colors to perfection allowed me to change the way I approached creating my work. But as I started to participate in more events and create zines the time and energy needed for that level of perfection was beginning to no longer be feasible. Enter the Risograph and my practice was completely revolutionized. I still got the vibrancy of color I craved from silkscreen but with a speed that aided my production timelines.
A project that could take me 2 days with silkscreen could be achieved in an afternoon with Riso. But that level of perfection and control from screenprinting was something I had to accept letting go of. I had to be ok with accepting misregistration and sometimes quirky results. Adapting what Riso was capable of, and discovering what I was capable of achieving within the confines of pushing this medium. Working smarter not harder.
Just like people, Risograph is a little quirky, and imperfect, that’s its nature. Riso taught me to accept my imperfect self and release my control to the chaotic fun you can have with these colors. Informing my philosophy toward print, “Riso will never be perfect, but frankly neither will I”.
Riso Philosophy, 2019
Flo Pink (2x), Yellow, Seafoam, and Blue on White paper
Tire Marks
Paper is pulled into the Riso by a toothed rubber roller giving sheets the initial momentum into the press and under the color drum.
Risograph ink dries quickly to a lightly powdery finish, but has a tendency to transfer pigment while still fresh. It can also be reactivated with firm pressure or the oils in your skin.
When feeding a piece through for multiple colors the rubber roller can accumulate residual pigment from previous layers and create small horizontal lines in the center of some images. These are called tire marks, this example shows them on the U, N, and S.
Tire marks, smudges, or a stray finger print are all erasable from surfaces without ink (bare paper). I take preventative measures during my print production process to decrease their appearance but at times are an unavoidable factor of the medium.
Misregistration
When printing at full speed a Risograph printer can output roughly 100 prints per minute, but that speed easily creates chances of imperfections when lining up multiple color layers. This example shows yellow misregistered to blue.
It takes a trained eye to manually make micro-adjustments (registering) to best align the layers while the prints are moving through the machine.
With an average loss of 20-30% to this factor I embrace moments of misregistration that lend themselves to individual pieces as it shows the nature of the medium and choose to include them for sale.